From 2024 to 2025: Key Construction Industry Trends to Watch
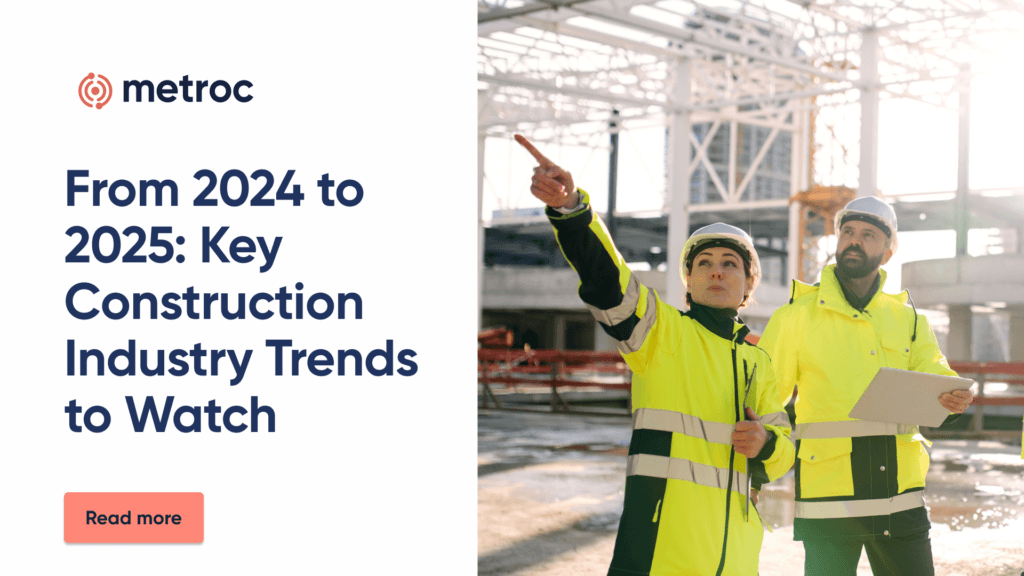
Change has become the pulse of construction, surging forward with technological leaps, a renewed focus on sustainability, and smarter project management. In 2024, groundbreaking tools like AI and BIM redefined project execution, offering fresh wins and new puzzles for industry players. The push for greener, modular solutions gained ground, making adaptability the currency of staying ahead.
Yet, 2024 wasn’t without its share of bumps. High costs of innovation, dwindling skilled labor, and unpredictable supply chains called for some creative maneuvering. These hurdles taught valuable lessons that are now blueprints for what’s next.
As 2025 edges closer, the big question is: how will these lessons fuel the next wave of trends? This article looks into 2024’s defining moments, the insights gained, and how they set the stage for navigating what’s on the horizon.
Key Trends Defining the Construction Scene in 2024
Technological Advancements

Technological advancements are driving significant changes in the construction industry, shaping the way projects are designed, managed, and executed.
Building Information Modeling (BIM) is one of the most impactful tools transforming the industry. BIM creates detailed 3D models that not only visualize a project but also streamline collaboration between architects, engineers, and contractors.
These shared models help reduce communication gaps and minimize design errors, which leads to fewer delays and more efficient use of resources. By improving material estimation, BIM also supports sustainability efforts, helping you cut waste and lower costs.
Artificial Intelligence (AI) is another game-changer. AI is increasingly used for design optimization, project management, and predictive analysis. Generative AI, in particular, can quickly produce multiple design options, giving you more innovative solutions to choose from and speeding up the decision-making process.
AI can also improve project scheduling, cost estimation, and risk management by providing data-driven insights.
Additionally, predictive maintenance powered by AI ensures better equipment performance, reducing costly downtime.
Drones and robotics are making their mark in construction as well. Drones are used to perform site surveys, gather real-time data, and create detailed maps, all of which improve monitoring and boost project accuracy. They reduce the need for workers in potentially dangerous areas, improving safety on-site.
Robotics, meanwhile, are being integrated for tasks like bricklaying and concrete pouring, increasing productivity and cutting down on manual labor. By automating repetitive or hazardous jobs, robotics can also help address the ongoing workforce shortages in the industry.
Companies to keep an eye on:
- Make a BIM (Finland): Founded in 2023, Make a BIM leverages AI to generate digital models of existing buildings by converting 2D drawings into BIM models within minutes, significantly reducing manual labor and enhancing efficiency.
- Infrakit (Finland): Infrakit offers a cloud-based platform that integrates BIM and GIS data, facilitating real-time collaboration and data sharing among construction project stakeholders.
- XYZ Reality (UK): XYZ Reality has developed an augmented reality headset that enables construction workers to view holograms of BIM models on-site, facilitating precise construction and reducing errors.
- KTV Working Drone (Norway): KTV Working Drone specializes in high-rise window and facade cleaning using drones, offering a safer and more efficient alternative to traditional methods.
- Drone Volt (France): Drone Volt is a French company that designs and manufactures professional drones for various industries, including construction. Their drones are used for tasks such as inspection, surveillance, and mapping, enhancing efficiency and safety on construction sites.
Sustainability and Green Building Practices

Sustainability and green building practices are no longer optional in the construction industry, they are essential. As environmental regulations tighten and clients prioritize eco-friendly solutions, you need to stay ahead by adopting materials and designs that reduce environmental impact while improving project value.
One of the major shifts in 2024 centers on eco-friendly materials. Construction is moving towards using renewable, sustainable resources like recycled steel, bamboo, and eco-concrete. These materials help reduce the carbon footprint and align with green building certifications, such as LEED and BREEAM.
By choosing materials that are renewable or have a smaller environmental impact, you can attract environmentally conscious clients and gain a competitive edge in the market.
At the same time, energy-efficient designs are being adopted across the industry. You’ll notice a growing emphasis on strategies that cut energy consumption, such as passive solar design, which uses the building’s orientation and materials to regulate temperature naturally.
In addition, high-performance insulation plays a critical role in minimizing energy loss, leading to lower operational costs for building owners. The integration of smart systems and IoT technology is also becoming more common, allowing for real-time energy management.
There’s also a strong push towards net-zero energy buildings, which produce as much energy as they consume. These structures align with global sustainability goals and can help you comply with increasingly strict energy regulations.
Net-zero energy designs are not just beneficial for the environment; they also reduce long-term operating expenses for your clients, creating a compelling selling point.
Sustainable materials and energy-efficient designs are driving the future of construction.
Companies to keep an eye for:
- ecopals (Germany): ecopals focuses on sustainable road-building materials by converting waste into eco-friendly construction products, contributing to greener infrastructure development.
- Aedifion (Germany): Aedifion offers a platform for the digital decarbonization of buildings, optimizing energy consumption and enhancing sustainability through advanced data analytics.
- Betolar (Finland): Betolar develops low-carbon construction materials by utilizing industrial side streams, offering sustainable alternatives to traditional cement.
- Aisti (Finland): Aisti produces sustainable acoustic tiles made from wood fiber, which are carbon-negative, recyclable, and plastic-free, contributing to greener building interiors.
Modular and Prefabricated Construction

Modular and prefabricated construction is becoming a significant trend in the construction industry in 2024. This method is gaining traction because it offers practical solutions for speeding up projects and reducing costs, while also improving quality control.
Modular construction involves assembling building components off-site in a controlled environment. This process allows for standardized production, which speeds up timelines and ultimately cuts down on both labor and material costs.
Manufacturing parts in a factory setting minimizes on-site construction activities, which can lead to fewer disruptions and delays. The predictability of modular construction makes it easier to meet deadlines and stick to budgets.
One key benefit you’ll notice is the cost-effectiveness. Since modules are built to standardized specifications, economies of scale come into play. This reduces the overall cost per unit, making modular construction an attractive option when you need to be mindful of project budgets.
Additionally, because the assembly happens in a factory, the weather or other external conditions rarely affect timelines, which further limits cost overruns.
Another major advantage is quality control. Factory environments ensure precision and repeatability, meaning you can expect consistent quality throughout the project. Since the components are produced under controlled conditions, errors are minimized, and there’s less variability compared to traditional on-site construction.
This process also significantly reduces material waste, which leads to both cost savings and a positive environmental impact. Prefabrication allows you to use materials more efficiently, cutting down on excess waste that would typically occur during conventional construction.
In adopting modular and prefabricated methods, you also contribute to sustainability efforts by reducing on-site waste and energy consumption. The controlled setting of a factory allows for more accurate material use, helping you align with green building practices.
Modular construction provides both efficiency gains and improved quality control.
Companies to keep an eye for:
- Flow Modules (Finland): Flow Modules focuses on industrializing housing production by improving construction processes and product prefabrication, enabling cost-effective apartment building construction.
- Modulous (UK): Modulous offers a new approach to increase home production by providing a platform that enables the design and delivery of modular homes without the need for factories.
- Logiprefab (Lithuania/Norway): Combines advanced production technology with modern construction methods to produce economical and sustainable panel-frame and modular turnkey houses inspired by Scandinavian traditions.
The Tough Side of Staying on Trend

High Initial Investment Costs
High initial investment costs present a significant barrier for many companies in the construction industry, particularly when it comes to adopting new technologies. Advanced tools like AI-driven project management systems, drones for site inspections, and Building Information Modeling (BIM) software can offer considerable long-term benefits. However, the upfront capital required to integrate these technologies can be prohibitive.
Smaller construction firms often struggle to allocate the necessary budget to keep up with larger enterprises, which can more easily absorb the financial impact of investing in cutting-edge tools. The cost of acquiring new technologies doesn’t stop at just purchasing the hardware or software. You also need to consider:
- Training employees on how to use these systems effectively.
- Integration costs, which can involve modifying current workflows and updating existing infrastructures.
- Ongoing maintenance and support for the new technologies.
These factors compound the initial financial pressure, making it even harder for smaller firms to justify the expense when they’re already operating on tighter margins.
Another key concern is the return on investment. While the long-term benefits of implementing advanced technologies are clear—such as increased efficiency and reduced project timelines—there is often a lag before those benefits materialize. This delayed ROI, combined with unpredictable market conditions, makes it risky for many firms to commit large sums of capital. The uncertainty surrounding when or if the investment will pay off can be enough to deter companies from taking the plunge.
Workforce Shortages and Skill Gaps
Workforce shortages and skill gaps present a significant challenge for the construction industry in 2024. As experienced workers retire and fewer young professionals enter the field, you might find it increasingly difficult to keep up with the demands of modern construction projects.
An aging workforce is a primary factor. Many experienced workers are nearing retirement, and the industry is struggling to replace them with younger talent. This generational gap exacerbates the already existing shortage of skilled labor.
In Sweden, it’s estimated that 10% of the construction workforce will retire by 2028. While there will only be a modest increase of 88,000 posts in Europe from 2022 to 2035, 4,127,000 people are expected to leave the field over that time according to Cedefop Skill forecast.
As fewer younger individuals pursue careers in construction, the skills gap widens, making it harder for companies to adopt new technologies and methods.
Beyond the general labor shortage, there’s also a growing need for specialized skills. Advanced construction methods, such as using drones for site surveys or implementing Building Information Modeling (BIM) software, require workers with very specific expertise.
Companies face two main options here:
- Train existing employees to acquire these new skills, or
- Hire specialized workers who are already proficient.
However, both approaches come with challenges. Training current staff can be time-consuming and costly, while hiring skilled professionals is difficult because of high competition and limited availability.
The shortage of skilled labor has a direct impact on project timelines and overall efficiency. With fewer qualified workers available, you might experience project delays, missed deadlines, and increased costs. Additionally, without the right skills, your company might struggle to integrate new technologies, putting you at a competitive disadvantage.
The shortage of skilled labor in 2024 challenges both project timelines and tech adoption.
Supply Chain Disruptions and Material Costs
Supply chain disruptions and material costs remain critical factors impacting the construction industry in 2024. These issues can lead to delays, budget overruns, and even jeopardize project feasibility. Understanding the ongoing challenges and how to maneuver through them is important.
Ongoing supply chain issues continue to affect the availability of essential construction materials. Global events like geopolitical conflicts, trade restrictions, and pandemics still cause delays in shipping and production, which can slow down the timely delivery of materials. This can result in extended project timelines or missed deadlines, making it difficult for firms to meet client expectations.
Adding to the challenge is the volatility in material prices. For materials like steel, cement, and lumber, prices fluctuate frequently. This unpredictability makes it harder for contractors to plan budgets effectively.
Volatile costs can strain project budgets and negatively affect profitability. For example, a sudden increase in the price of steel could turn a previously viable project into a financial risk.
Some construction firms have adopted strategies to cope with this uncertainty. These strategies include:
- Early procurement: Buying materials early helps companies lock in prices before they spike, but this requires upfront capital and storage solutions.
- Supplier diversification: Working with multiple suppliers from different regions can reduce the risk of relying on a single source, though it can also increase logistical complexity.
- Long-term contracts: Negotiating longer-term agreements with suppliers can help stabilize material costs, but these contracts might come with trade-offs in flexibility.
Each of these approaches can mitigate risk, but they require careful financial and operational planning.
Material cost volatility and supply chain disruptions can make or break a construction project’s timeline and profitability.
Tackling these industry challenges means being equipped with the right tools for precise decision-making. High initial investment costs may seem daunting, but they are necessary for staying competitive—and Metroc is here to make those investments worthwhile.
Our data-driven platform equips you with comprehensive project insights and analytics to assess ROI and make informed, strategic decisions for long-term success. With labor shortages, targeted insights ensure you focus on high-impact projects that maximize your team’s efforts. Real-time updates and project data empower proactive planning, making procurement and supplier diversification smoother to mitigate delays and budget risks seamlessly.
Construction trends in 2025

Advanced Technologies and AI Expansion
As we move forward, the role of advanced technologies and AI in construction is set to grow significantly. AI’s integration will extend beyond its current uses, becoming a core component of project management and decision-making processes. You’ll see AI-driven predictive analytics becoming important for optimizing project timelines. With real-time data feeding into these systems, stakeholders will be able to adjust plans instantly and improve overall efficiency.
AI will also enable you to make data-driven decisions, helping teams manage risks and streamline operations. Advanced analytics will allow you to predict potential bottlenecks or delays and address them before they become an issue. Automation tools will handle repetitive tasks, freeing up human resources for more complex challenges.
Robotics and automated machinery will continue addressing labor shortages, taking over tasks that require precision and repetition. This will not only improve the speed of construction projects but also improve accuracy, reducing human error and rework.
Companies to keep an eye on:
- CubiCasa (Finland): CubiCasa offers AI-powered solutions for creating accurate floor plans and property data, streamlining the real estate and construction documentation process.
- Builderhead (Finland): Builderhead offers a modern project management software tailored for the real estate and construction industry. Their platform integrates people, projects, tasks, and essential tools, facilitating efficient project development and execution.
- Spacemaker (Norway): Spacemaker utilizes AI to optimize building designs by analyzing millions of solutions for architectural and environmental factors, enhancing decision-making in the early stages of construction projects.
Enhanced Sustainability and Carbon-Neutral Initiatives
Construction firms will intensify efforts toward enhanced sustainability and carbon-neutral initiatives in 2025. Governments, consumers, and industry leaders are pushing for construction practices that reduce environmental impact. This trend builds on the progress made in 2024, when the industry began to embrace more eco-friendly materials and energy-efficient construction processes.
One key driver of this shift is access to data. The ability to source eco-friendly materials accurately depends heavily on having reliable data. With the right information, you can ensure that your projects meet strict regulatory standards while also aligning with broader sustainability goals. This is especially critical as environmental regulations become stricter, and compliance is non-negotiable for firms that want to remain competitive.
Another important factor is automated reporting, which is becoming a necessity for construction companies aiming to stay in line with global environmental targets. Automated systems can provide regular updates on regulatory changes and help you adjust your strategies without delays. This allows firms to maintain both compliance and operational efficiency, instead of getting stuck by manual processes.
Finally, data-backed decision-making is set to play an important role in 2025. With real-time analytics, you can monitor your sustainability efforts and track key metrics such as carbon output and material sourcing. This means you can adapt your strategy dynamically as new challenges arise, ensuring you remain on course to meet your sustainability targets.
Companies to keep an eye on:
- Paebbl (The Neatherlands): Paebbl specializes in decarbonization technology that transforms captured CO₂ into carbon-storing construction materials, providing a sustainable alternative to conventional cement.
- Cemvision (Sweden): Cemvision develops low-carbon cement alternatives, aiming to reduce CO₂ emissions in the construction industry by up to 95% compared to traditional methods.
Addressing Urbanization with Innovative Solutions

Urbanization is rapidly increasing, and by 2025, construction companies will need to address the growing demand for smart, efficient, and scalable buildings. As more people migrate to cities, the pressure to create urban environments that are livable, sustainable, and adaptable will intensify. Europe’s urbanization level is projected to rise to around 83.7% by 2050, and built-up areas are expected to expand by more than 3% between 2015 and 2030, covering 7% of the EU territory by 2030.
To keep pace with this demand, access to detailed project data and stakeholder information will become important. You need to understand not only the physical aspects of construction but also the social and economic dynamics of urban development. Having real-time access to this information allows you to make timely decisions, ensuring that projects are both relevant and sustainable in the long term.
Managing urban projects effectively also requires real-time project tracking. Urban projects tend to be highly complex, often involving multiple contractors, government regulations, and tight deadlines. Real-time tracking helps reduce delays, avoid cost overruns, and ensure compliance with local regulations.
Opportunities in urban construction can change rapidly. To stay ahead, it’s key to utilize advanced search filters and automated updates. These tools allow you to quickly identify new projects, monitor regulatory changes, and respond to emerging trends, giving you a competitive edge in a crowded market.
Companies to keep an eye on:
- Raxalle (Finland): Raxalle automates workforce management processes on construction sites, saving time and money for main contractors by streamlining daily site operations related to workforce management and supervision.
- Findable (Norway): Findable offers a platform that digitizes and organizes building documentation, improving accessibility and efficiency in managing construction projects, particularly in urban settings.
- NREP (Denmark): NREP focuses on urban development projects that integrate sustainability and innovation, creating adaptable and efficient urban spaces to meet the demands of growing city populations.
Strategic Moves to Get Ready for 2025

Financial Planning and Phased Investments
Strategic financial planning is important for construction firms aiming to stay competitive. With rising costs and increasing pressure to innovate, a solid financial approach ensures that your company can invest in new technologies and trends without overextending its budget.
One effective method is to adopt phased investment approaches. Instead of committing large sums of capital upfront, breaking down investments into smaller, manageable phases helps you control costs. This step-by-step approach allows you to implement new technologies or practices gradually, so you can test them on a smaller scale before full deployment.
As a result, you reduce risk and can more easily adapt to varying market conditions or changes in your company’s financial capacity. Phased investments also offer flexibility, enabling you to adjust your spending based on emerging trends or unforeseen challenges.
In addition to phased investments, forming strategic partnerships can be a game-changer. Collaborating with technology providers, suppliers, or even other companies within the construction industry can lower costs by sharing both financial burdens and expertise. These partnerships often provide access to resources that would be difficult or expensive to secure independently.
For example, co-developing innovative solutions with a partner can improve your company’s competitiveness, allowing you to stay ahead in a rapidly evolving market. Also, partnerships foster knowledge-sharing, which levels the playing field for smaller firms that might lack the resources of larger competitors.
By blending phased investments with strategic collaboration, you position your company to thrive in 2024 without taking on unnecessary financial risk.
Phased investments and collaboration reduce costs while boosting flexibility.
Workforce Training and Development
As new technologies and methods reshape how projects are managed and executed, companies need to ensure their teams are equipped to handle these changes. There are two main strategies to focus on: upskilling the current workforce and attracting new talent.
First, investing in training programs to upskill your existing employees can provide significant returns. Training your workforce to master new technologies, like Building Information Modeling (BIM) software or AI-driven project management tools, directly increases productivity. When employees are better prepared to operate advanced machinery or use cutting-edge software, they work more efficiently and with fewer errors.
Moreover, offering tailored training programs for specific roles or technologies ensures that your team is versatile and adaptable. This fosters a culture of continuous learning and innovation, which is important to staying competitive.
Training both the current workforce and new hires is important for long-term success in construction.
Attracting and retaining young talent is another key focus. With an aging workforce and increasing demand for skilled labor, the construction industry needs to appeal to younger demographics. Offering competitive salaries and modern work environments helps.
However, what really draws younger workers is the chance to engage with advanced technologies and grow within the industry. Highlight your company’s use of digital tools and automation when recruiting tech-savvy candidates. Once hired, mentorship programs and clear career progression paths can increase retention. This reduces turnover, creating a more stable and skilled workforce over time.
Diversified Supply Chain Management
Supply chain disruptions can quickly derail a project, leading to delays and increased costs. To minimize these risks, diversified supply chain management is important, and there are two key strategies to focus on.
Supplier diversification strategies help reduce the impact of potential disruptions on project timelines. Relying on a single supplier can leave you vulnerable if they face issues like production delays or shortages. By building relationships with multiple suppliers—both local and international—you create a safety net that ensures a steady flow of materials.
Diversifying your supplier base can also lead to more competitive pricing, as multiple options give you utilize when negotiating costs. Additionally, sourcing from various regions helps mitigate risks caused by regional supply shortages or transportation bottlenecks.
Early procurement planning is another critical element. By securing key materials well in advance, you can avoid price fluctuations and supply delays that could slow down your project. This approach aligns with better project scheduling and budget management because it keeps your timeline and costs predictable.
To make early procurement successful, you’ll need a robust forecasting model that accurately predicts future material needs based on project scope and market conditions. With this strategy, you’ll be in a better position to respond to unexpected disruptions, helping maintain project momentum.
Supplier diversification and early procurement are important to reduce risks and keep projects on track.
Final Thoughts: Bridging 2024 Trends to 2025 Success
The construction industry trends of 2024 set a strong foundation for understanding what’s to come in 2025. Key advancements in technology, sustainability, and modular construction defined the current landscape while challenges like high investment costs, workforce shortages, and supply chain complexities highlighted the need for strategic planning. Looking forward, embracing innovative technologies, boosting sustainability efforts, and addressing urbanization will be crucial for maintaining growth and resilience.
Staying ahead in the construction industry requires not just overcoming challenges but capitalizing on strategic opportunities. As a comprehensive platform that provides detailed property insights, stakeholder information, and advanced CRM capabilities all in one place, Metroc empowers you to do just that, enhancing predictability and offering real-time data to keep you informed about upcoming opportunities.
By helping you zero in on the most lucrative projects, Metroc supports effective decision-making, particularly when workforce shortages make resource allocation essential. With tools designed to improve supply chain management and identify high-impact projects, our platform positions you to navigate complexities and achieve sustainable growth.
Interested in maximizing your construction project potential? Book a demo today to see how Metroc can elevate your strategic planning and operational efficiency.
FAQ
What key construction industry trends are expected for 2025?
In 2025, continued advancements in AI and robotics will further optimize project timelines and resource allocation. Enhanced sustainability initiatives and carbon-neutral practices will become more prominent, driven by regulatory demands. Urbanization will also push for more innovative, scalable, and adaptable construction solutions.
How will sustainability evolve in the construction industry by 2025?
Sustainability efforts will intensify, focusing on carbon-neutral construction practices and improved energy management. Firms will leverage real-time data and automated reporting to meet stricter environmental regulations, ensuring compliance and operational efficiency.
What challenges from 2024 will carry into 2025?
Workforce shortages and supply chain disruptions are expected to persist into 2025. Companies will need to address these issues by improving workforce training, diversifying supplier networks, and implementing early procurement strategies to stay resilient.
What is driving the adoption of advanced technologies in 2025?
The push for efficiency and cost-effectiveness will drive the increased adoption of AI, robotics, and predictive analytics in 2025. These technologies will help optimize project management, improve decision-making, and automate repetitive tasks, reducing labor dependency and errors.
How can construction firms prepare for 2025 trends?
Strategic planning, phased investments in new technology, and workforce training are key. Firms should focus on enhancing supply chain resilience and using data-driven insights to identify high-impact projects and manage risks proactively.